Summary:In the actual CNC machining process, it will be found that the same CNC lathes are operated by diffe...
In the actual
CNC machining process, it will be found that the same CNC lathes are operated by different personnel, and the efficiency varies greatly within the same time. The capabilities of many CNC lathes cannot be fully reflected and cannot play their optimal role. In the process of use, only by fully considering all the factors affecting the CNC lathe, can the capabilities of the CNC lathe be brought into full play:
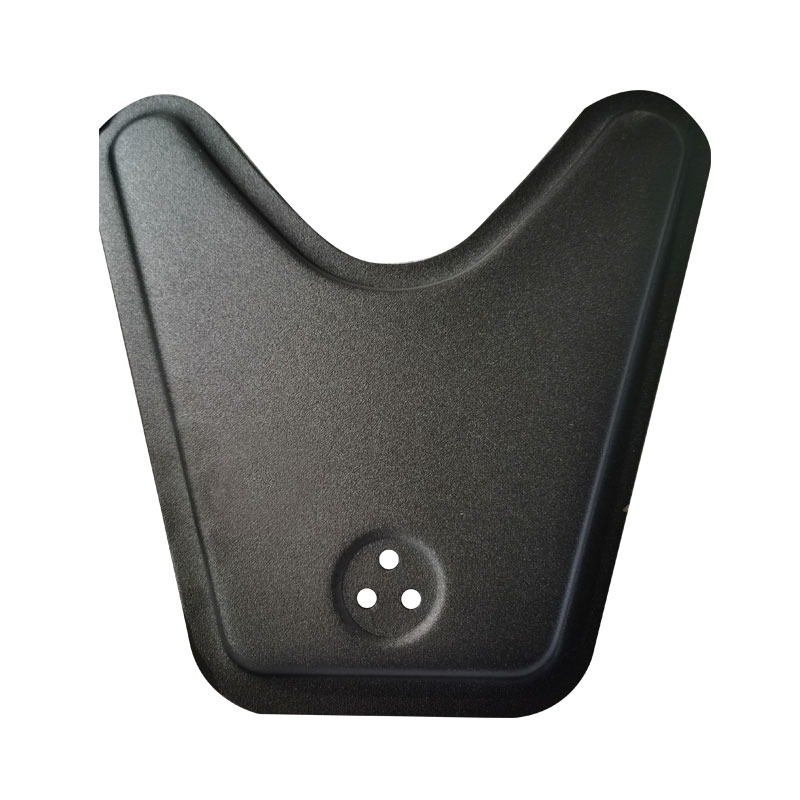
1. The formulation of CNC machining process
Usually a part can have several different processes. The process of the part is different, and its production efficiency, processing cost and processing accuracy are often significantly different. Therefore, we should ensure the quality of the part processing, according to the specific conditions of production, Try to improve production efficiency and reduce production costs, and formulate a reasonable CNC machining process.
2. Choose the right tool
The selection of tools should consider the processing capacity, process content, workpiece material and other factors of the CNC machining center. The tool selected by the high-speed machining center not only requires high hardness, high wear resistance, sufficient strength and toughness, high heat resistance and good manufacturability, but also requires stable dimensions and convenient installation and adjustment. Therefore, new high-quality materials should be used to manufacture CNC machining tools, and the tool parameters should be optimized to make the size of the tool adapt to the surface size and shape of the workpiece to be machined.
3. Reasonably determine the tool setting point
The tool setting point is the starting point of the tool movement relative to the workpiece when machining the part on the CNC machining center. Also known as "program starting point" or "starting point". The selection of tool setting points must comply with the following principles: easy to use digital processing and simplified programming; easy to align on the machine tool, easy to check when processing; small processing errors. The position of the tool setting point can be selected on the workpiece or outside the workpiece (such as a fixture or a lathe), but it must have a certain dimensional relationship with the positioning reference of the part. The tool setting point should be selected as far as possible on the design datum or process datum of the part, such as the workpiece positioned by the hole, the center of the hole can be selected as the tool setting point. The position of the tool is aligned with this hole, so that the "positioning point" coincides with the "tool setting point". In this way, it is possible to better improve the efficiency of tool setting and ensure the processing quality.
4. Use special lathe cutting oil to reduce tool wear
The lathe cutting oil contains special additives for cutting, and the release of the additives can effectively protect the tool, reduce the wear of the tool and improve the accuracy of the workpiece. By reducing the number of tool changes to increase the running time of the equipment, the efficiency is greatly improved.
5. Reasonable selection of cutting amount to improve the cutting efficiency of machining allowance
When selecting the cutting amount of the CNC milling machine, if it is rough machining, it is generally to improve efficiency, but economy should also be considered, and a larger depth of cut and feed speed can be selected; if it is semi-finishing and finishing, it should be ensured On the premise of quality, efficiency and economy should be taken into account; the feed speed should be set as high as possible when the tool does idle motion.
6. Flexible use of various auxiliary functions of CNC lathes.