Summary:
Why choose forgings? Forgings have many applications in life. Compared with castings, the valve bod...
Why choose
forgings? Forgings have many applications in life. Compared with castings, the valve body of forged valves has a more uniform structure, better density, better strength integrity, better dimensional characteristics, and smaller dimensional errors. The directional structure (pipeline) has higher performance than castings in terms of overall strength and stress. Forgings need to be consistent with each piece, without any porosity, excess space, inclusions or other defects. The components produced by this method have a high ratio of strength to weight. Next, I will introduce to you the excellent performance of forgings.
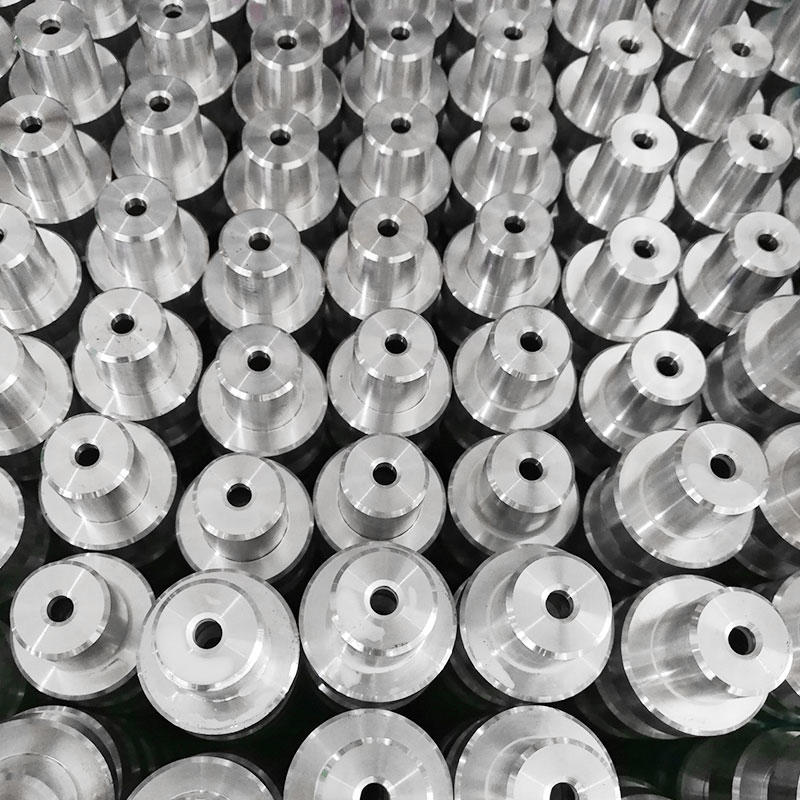
1. High strength
Hot forging promotes crystallization and grain refinement, so that the material can achieve the greatest possible strength and consistency, and the variation from part to part is minimal. The particle flow precisely follows the contour of the valve body. These continuous streamlines help reduce the incidence of fatigue or common failures.
2. Reliability
The forging property that can meet the requirements of the design structure has always been one of the most important advantages of forgings, and to a certain extent lies at the top of the above-mentioned characteristics.
3. Structural integrity
Forging eliminates internal defects, produces a consistent metallographic structure, and ensures excellent performance. Where the stress and corrosion problems in the crystal are serious, the forgings can guarantee a long service life and trouble-free service.
4.Consistency
The dimensional consistency of closed-die forging results in complete control of the key wall thickness, avoiding defects caused by core displacement in the casting process, and ensuring that there are no internal defects through high-quality, non-separated steel ingots and the impact of 10,000 to 30,000 tons of presses , A consistent metallographic structure.